Industrial Epoxy Floor Coating Contractors
An Industrial Floor Surface as Hard as Nails
As the manager or owner of a warehouse, factory, storage facility, or other industrial building, some of the most important considerations you make on a daily basis include worker health & safety, building maintenance costs, and production efficiency - industrial epoxy flooring can help with all of this.
We install, refinish, or repair industrial floors, and we also offer commercial paint coatings for ceilings and walls. We use 100% solid, commercial-grade epoxy with zero volatile organic compounds (VOCs), which is the perfect solution for an industrial or warehouse floor, because:
- 100% solid epoxy creates a harder, longer-lasting finish than other flooring solutions
- Zero VOC epoxy is essential in an environment where workers are constantly exposed to the industrial floor
- Non-flammable
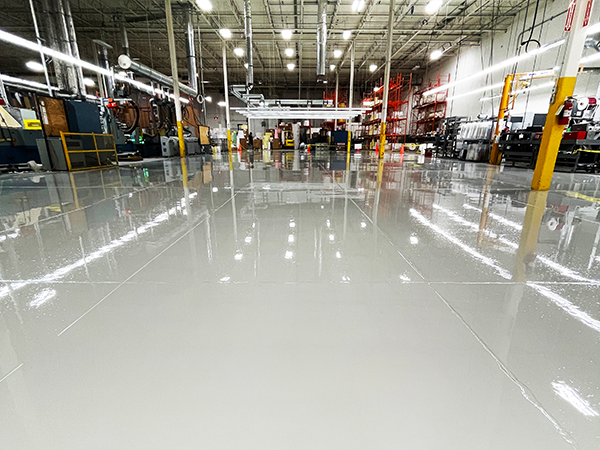
Epoxy Warehouse & Industrial Floor Coating Essentials
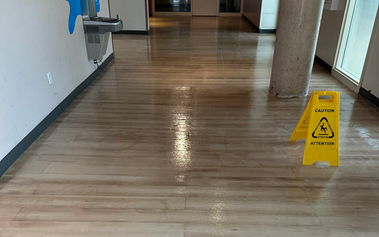
Solid, Safe, & Clean Epoxy
Meet Health & Safety Guidelines
In a warehouse or factory environment, it’s essential that your workers have a non-slip surface made with zero VOCs to prevent any dangerous fume inhalation while working. You can increase traffic flow and efficiency on the floor, all while making sure workers are mindful of safety protocols.

Superior Durability
Hold Up Under Pressure
Industrial epoxy flooring can hold up under the weight and pressure of uncommonly heavy machinery in ways that other flooring solutions simply can’t. If your floor has factory production machines, large appliances, or anything big & heavy, you need an epoxy floor that won’t crumble under the pressure.

Coving
Make Cleaning Easier
On a warehouse or factory floor, mold, bacteria, dirt, and mildew all find a way into the hard-to-clean areas and build up over time, creating hazards for your workers, and wearing down your floor faster. The coving technique continues the epoxy 4-6” up the wall, which makes cleaning easier and keeps your building a safer place to work.
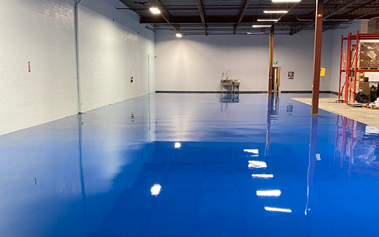
Longer-Lasting Material
Lower Long-Term Costs
A 100% solid, commercial-grade epoxy is the only material strong enough to hold up under the pressure from forklifts, pallet jacks, heavy machinery, and constant foot traffic. Any solvent-based epoxy, water-based epoxy, or non-epoxy flooring material will be too thin to last long-term, and will show wear and tear on the production floor much faster.
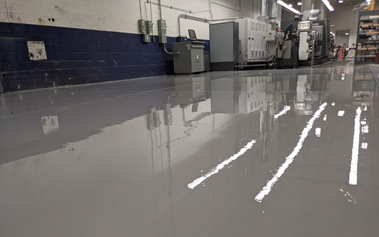
Resistant Environment
Control Chemicals, Conductivity, Dust, & Static
Industrial epoxy flooring can control and resist a number of irritants in your environment. It offers better dust and static control, is chemically-resistant, and improves conductivity. If you’re running an environment with any static, electricity, chemicals, or dust, the epoxy floor will reduce these hazards, increase production uptime, and create a safer, more resistant environment for your workers and machinery. Feel free to contact us about any unique flooring solution needed.

Safety Lines & Stickers
Reinforce Your Protocols
On a factory floor, safety is critical, and we can apply long-lasting safety lines or decorative stickers to your epoxy floor finish. These will remind staff about any safety protocols you have for the floor, and will last as long as the floor without ruining the finish. You can choose & customize the colours to match your brand or building ambiance.
Why Work with Toronto Epoxy Pros?

Industrial Epoxy Floor Experts
Our industrial epoxy floor contractors have over 15 years of experience working with warehouse, factory, storage, and other buildings, and we’re certain we can determine the right procedures for your unique industrial building based on our previous project experience.

Eco-Friendly Epoxy
For an eco-friendly warehouse floor coating option, opt for our zero VOC, 100% solid epoxy that will help meet industry health & safety regulations, and create a healthier environment for your workers.

Insured & WSIB-Certified
Our industrial floor coating contractors are Workplace Safety and Insurance Board-Certified, and are covered by $2-5 million in liability insurance, so you can be sure your project will be completed without any headaches or holdups.

Efficiency & Minimal Disruption
It’s difficult to shut down warehouse operations to have your floors epoxied. You can count on us to develop a schedule that ensures minimal disruption, while completing the project on time - even if that means we work on weekends or outside of business hours.

Competitive Pricing
If you shop around for another industrial epoxy flooring service, we’re certain you’ll choose us, as our high-grade equipment and past experience industrial project strategies will get you up and running fast, and shorten your project time compared to our competitors.

We Demonstrate Our Value
We’ll take the time to explain how an epoxy floor would benefit your unique industrial floor or building, and help you understand how this upfront investment will save you far more over the lifetime of the floor - far beyond the installation.
Industrial Building Epoxy Flooring Installation Process
The epoxy installation process involves four steps:
Patching & Smoothing
When a warehouse floor has any small or large cracks or defects, we patch them prior to applying the epoxy to make sure the final result is a perfectly smooth surface.
Grinding & Sanding
Proper industrial epoxy floor coating contractors will always diamond grind or sand the industrial floor prior to actually applying the epoxy, and you should skip over any company that skips this step. This opens up the pores on the surface and ensures the epoxy properly adheres to it. If your surface has extreme defects (like not being level), you may also need to parge the warehouse floor prior to epoxy application.
Industrial Vacuuming
We make sure the industrial floor is clear of all debris by cleaning the surface and removing all dust with an industrial vacuum- yet another step that cannot be skipped, as it will reduce the effectiveness of the epoxy’s final adhesion, and trap debris between the floor surface and the epoxy.
Epoxy Application and Drying
Once all this preparation has been done to the industrial floor, then we can apply the epoxy to the floor using squeegees and rollers. We then apply a second coat to ensure maximum thickness and ideal durability. After 24 hours, you can walk again on the warehouse floor, and after 48 hours, you can once again place heavy machinery or items like forklifts back on the surface, and then the coating will harden more over 7 days.
Patching & Smoothing
When a warehouse floor has any small or large cracks or defects, we patch them prior to applying the epoxy to make sure the final result is a perfectly smooth surface.
Grinding & Sanding
Proper industrial epoxy floor coating contractors will always diamond grind or sand the industrial floor prior to actually applying the epoxy, and you should skip over any company that skips this step. This opens up the pores on the surface and ensures the epoxy properly adheres to it. If your surface has extreme defects (like not being level), you may also need to parge the warehouse floor prior to epoxy application.
Industrial Vacuuming
We make sure the industrial floor is clear of all debris by cleaning the surface and removing all dust with an industrial vacuum- yet another step that cannot be skipped, as it will reduce the effectiveness of the epoxy’s final adhesion, and trap debris between the floor surface and the epoxy.
Epoxy Application and Drying
Once all this preparation has been done to the industrial floor, then we can apply the epoxy to the floor using squeegees and rollers. We then apply a second coat to ensure maximum thickness and ideal durability. After 24 hours, you can walk again on the warehouse floor, and after 48 hours, you can once again place heavy machinery or items like forklifts back on the surface, and then the coating will harden more over 7 days.
Industrial & Warehouse Epoxy Flooring Costs
Top 5 factors that affect the cost of an industrial epoxy floor installation
The cost to epoxy an industrial floor always depends on the epoxy type you choose, the square footage of the floor(s) to be covered, the amount of repair and other prep work prior to installation, and aesthetic options like colour and flake selection.
When trying to estimate the cost of your industrial epoxy floor coating, common variants that will affect the final cost are:
- The amount of patching, floor repair, grinding, and vacuuming to be done before the epoxy application. In warehouses, there is often grease or scuffs and divots - all of this must be repaired and cleaned to ensure your floor lasts for a long time.
- Improving the ambiance of the area with decorative flakes, colours, or safety lines.
- Adding coving, which helps particularly in warehouses or factories where items may fall on the floor, creating dirt or bacteria build up in corners.
- Increasing the number of epoxy coats or thickness, which is often necessary for floors that have heavy vehicles or machinery on them.
- Requiring overtime hours to meet extreme installation timelines.
How much does it roughly cost to epoxy a warehouse floor?
Our industrial epoxy floor application typically starts at $3.00 per square foot, and this is using our commercial-grade 100% solid epoxy. The cost per square foot can sometimes be lower if the square footage of the whole project is higher, or it can cost more if any of the factors above come into play.
Each industrial epoxy project is different, so discuss your project with one of our commercial epoxy floor professionals, who can provide an accurate estimate for you.
Industrial Epoxy Floor Installation FAQs
Is Toronto Epoxy Pros insured?
Yes, our epoxy application experts are certified under the Workplace Safety and Insurance Board (WSIB), and under our $2-5 million liability insurance coverage.
When is epoxy the right choice for an industrial building?
If you answer “Yes” to any of the following questions, epoxy is likely the right choice for your industrial building:
- Do the highest foot traffic area spots have deterioration or clear patterns where people are walking?
- Do you get a high volume of traffic (people constantly using the floor every day)?
- Do your floors need to be cleaned on a regular basis, especially to uphold industry standards or workplace safety conditions?
- Are there chemicals or harsh products being used in the area, offering potential opportunities for contamination?
- Do you have any up and down inclined areas or ramps being used frequently?
- Do you have a high utility bill that could be offset by floor coatings that reflect light and keep spaces more well-lit?
- Do you notice a lot of dust accumulation?
- Do you need markings on the floors for safety or to remind workers of protocols?
Why should you choose epoxy for your industrial floor?
You should choose epoxy flooring because it’s ideal for your industrial building, warehouse, factory, or storage facility by offering a hard, durable finish that will last for years to minimize long-term costs.
You’ll love the added health and safety features epoxy flooring can offer you such as:
- Improved conductivity and static control is essential for factory and warehouse environments
- Epoxy floors can hold up under the immense weight of heavy machinery and constant pressure in ways other floor types can’t
- Epoxy offers chemical resistance and prevents deterioration of the surface
- Anti-slip coating offers better traction for your workers and helps with fall-prevention
- Coving prevents mold and bacteria growth
- Easy-to-clean surface and dust reduction causes less buildup and cleaning time
- Rich colour or decorative flakes for added ambiance to improve worker morale
- Safety lines or stickers to reinforce safety protocols without ruining floor material
The easier your floor is to clean, the more likely it is to be cleaned regularly and correctly, which will avoid long-term damages or other upkeep issues in the building.
What other areas in my industrial building would benefit from epoxy flooring?
Here are some of the most common areas in an industrial building that greatly benefit from epoxy flooring:
- Production & Distribution Areas: Main warehouse floor, factory floor, product assembly line, shop floor, storage unit floors and hallways, receiving, storage, picking, packing, shipping
- Staff Common Areas: Break room, office, customer service, uniform change room, back hallways, restrooms, lockers
- Customer Self-Service Areas: Coffee/tea/water stations, snack areas, restrooms, waiting rooms
- Cleaning Stations & Facilities: Cleaning stations, cart storage, janitorial stations and rooms, laundry room, electrical/building maintenance rooms
- Interior Waste Disposal Areas: Garbage, refuse, grease, chemical disposal
- Loading Dock: Platform, stairs, connecting hallways
Which industries benefit the most from industrial epoxied flooring?
For industrial or commercial buildings, these industries very commonly choose epoxy:
- Automotive
- Chemical
- Electronics
- Factory production / assembly
- Food, beverage, and bakery facilities
- Hangers
- Operating theatre
- Parking garage
- Storage facilities
- Textiles
- Warehouse & logistics
How much downtime should I expect for industrial floor installation and drying?
In an industrial environment with a lot of foot traffic and heavy machinery, you should wait at least 24 hours before allowing your typical foot traffic back on the floor, and 48 hours before replacing the heavy machinery, appliances, or running forklifts across the surface. We recommend waiting up to 72 hours for next results whenever possible.
The actual time to install the epoxy after the patching, grinding, and vacuuming varies greatly depending on the square footage of the industrial floor, and the flooring system you have chosen. But in situations like an industrial building or warehouse floor where you have tighter windows to complete this project because you can’t shut down, we have experience from past projects that will help minimize the disruption to your business.
What exactly is epoxy?
Epoxy is a popular resin floor coating solution in large industrial spaces because of its long-lasting durability, superior strength below heavy machinery, ability to withstand constant foot traffic or forklifts, and its chemical resistance. Epoxy coatings are typically used on floor surfaces in commercial buildings because it is economical and ideal for large square footage surfaces.
Are all commercial-grade epoxies the same?
Commercial epoxies come in three different main types - solid, water-based, and solvent-based - each with their own unique properties. Which one you choose will affect the price, its durability, and the overall quality of the finished industrial floor. These are the main types and how they differ:
- 100% solid epoxy – Solid epoxy offers better durability because it is thicker and does not need liquids to evaporate (which also means it doesn’t contain harmful VOCs). Unlike other types that are also environmentally friendly (like water-based), solid epoxy still has an incredibly hard finish that’s still stain resistant.
- Water-based epoxy – A water-based epoxy is water soluble, but does not contain solvents. Unlike solid, you won’t get as hard of a finish or as long-lasting of a surface, but this type of epoxy is the most environmentally friendly.
- Solvent-based epoxy – Solvent-based is the oldest kind of epoxy, and requires solvents to evaporate while the surface dries. This creates a harder finish than you can get with a water-based epoxy, and will leave you with one of the hardest surfaces, however, because of the solvents, this epoxy has odours - some of which can be harmful - and is not recommended for any industrial building with a lot of people, or is not well-ventilated.
We only use 100% solid epoxy for industrial building floors (and all of our projects!), because it offers the most benefits, and is really the best type of epoxy on the market.